50㎛ Rare-Metal
世界初!50マイクロメートル
レアメタル極細線の製造に成功。
穴ダイス伸線が困難といわれるチタン、ニオブ、タンタルなどのレアメタルを当社独自の伸線加工方法により、従来は最小線径0.1ミリまで量産製品として製造しておりました。
しかし、レアメタルの極細線直径50マイクロメートルの製造依頼を受け、独自の製造機械及び製造ノウハウの研究開発の末、難加工材の極細線製造に成功。
レアメタル極細線は、医療、電子、繊維等での新製品開発の素材として今後大きな市場が期待されます。
さらに驚異の超極細線、直径25マイクロメートルへの開発に挑戦しております。
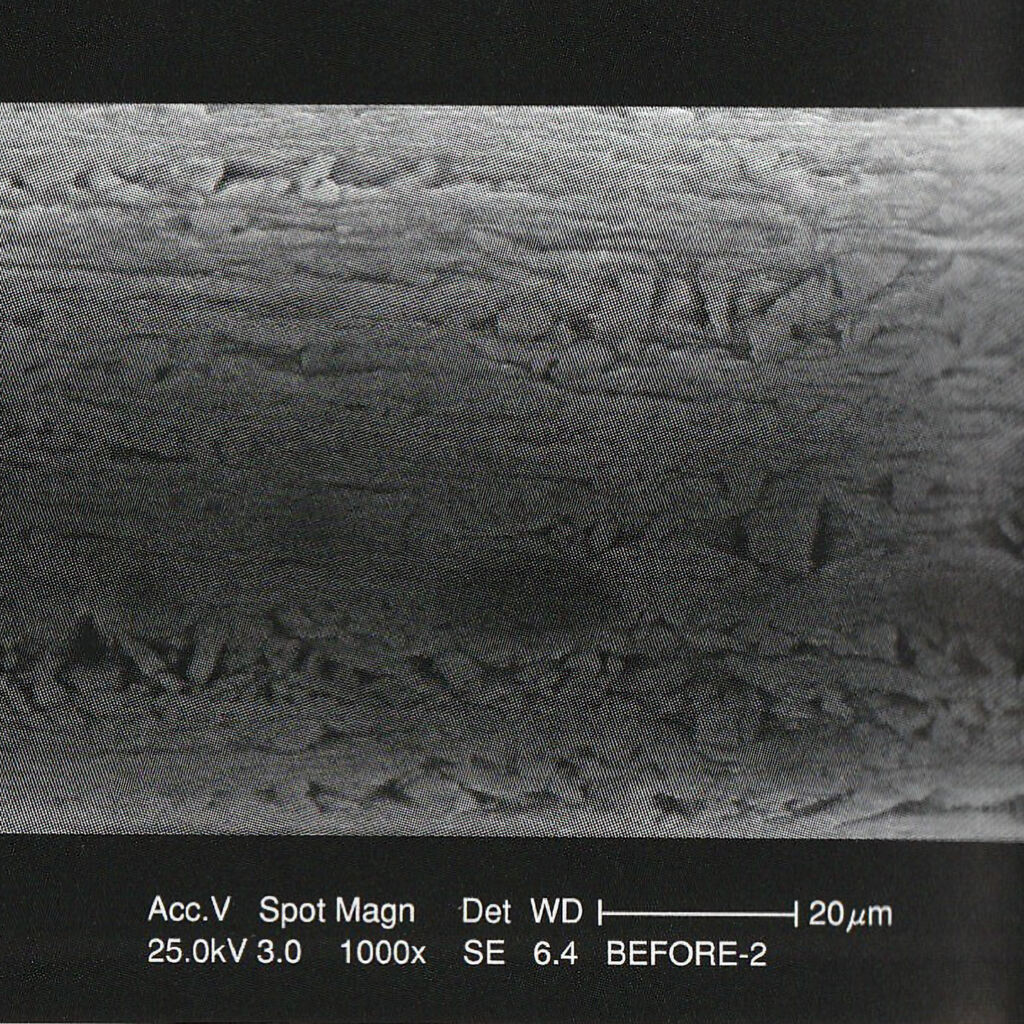
|医療機器用に開発されたレアメタル撚り線
Titanium wire rope woven with 7 and 7×7 strands made of Ti-10Zr alloy wirewith 50μm in diameter drawn using anodic oxidation.
7×7本撚り
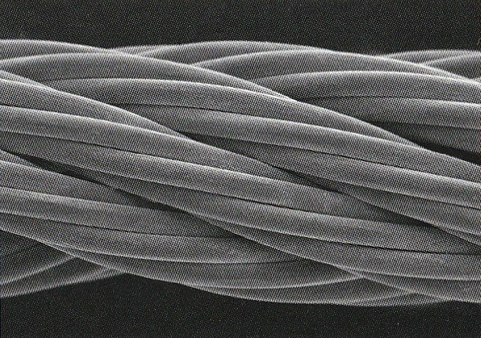
7本撚り
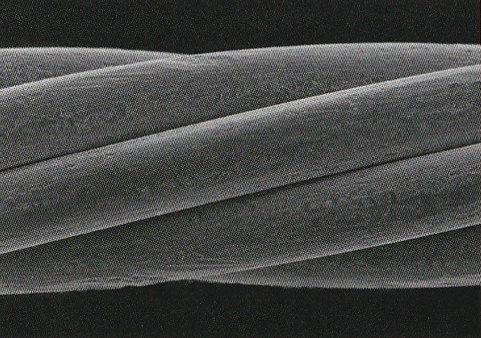
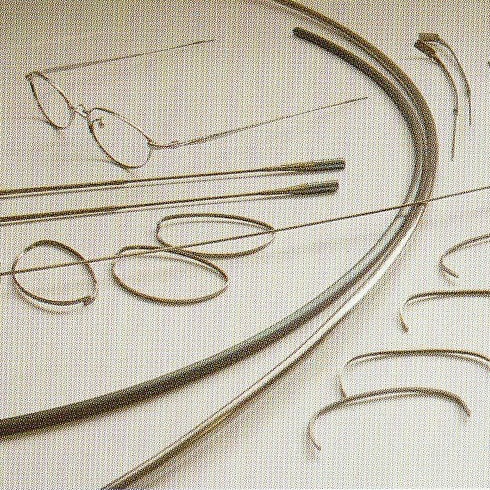
Products
レアメタル
~丸線(太線、細線)・異型線~
メガネフレームから医療器具まで、幅広い用途で採用されています。
当社では、チタン、ニオブ、タンタルなどのレアメタルを使用して、メガネフレーム・ゴルフクラブ・アクセサリー・医療・ハイテク部品・携帯のアンテナ・釣具・時計ベルト部分・剣道の面などに利用される、丸線(太線、細線)・異型線の伸線、圧延、金属研磨加工を行っております。
当社のレアメタル丸線は穴ダイス伸線のため、真円度0.0025ミリ以内で公差も±0.005ミリが可能です。また、通常は研磨、磨き仕上げですが、必要に応じて陽極酸化仕上げも可能です。
さらに、ある程度の硬度調整も出来ますので、電子部品には最適です。
Technology
独自の加工方法で、高精度の仕上がりを可能に
一般に線材の伸線加工としては、圧延とダイス伸線がありますが、圧延では、寸法精度に限界があるのと表面の欠陥が内部に隠されるため、精密さが要求され、表面の欠陥を嫌う場合は不適です。
当社が扱っているレアメタル(Ti Zr Ta Nbとその合金)線材は、ダイス伸線が非常に難しく、鉄や銅等と異なって金属地肌のままでは全く伸線できません。通常は、線表面に何等の被膜を作り、伸線加工を行った後、被膜の除去が必要となっておりました。
そこで当社では、独自の方法で被膜を作り、伸線加工後は極めて簡単に除去ができ、しかも表面を荒さない独自の被膜剤を開発し加工を行っております。
さらに独自の無酸化焼鈍、研磨、磨き、行程を備え、加工された線材を仕上げます。
寸法的にはΦ7.0~Φ0.05ミリまで伸線が可能で、精度的には±0.0025ミリまで仕上げ可能です。
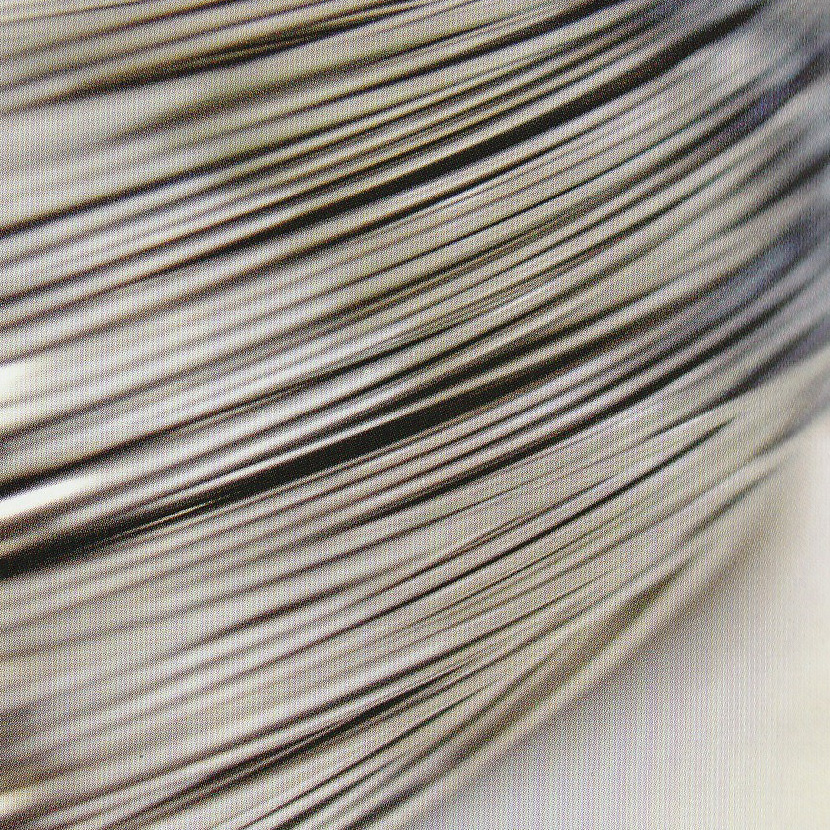
様々なニーズに応えるチタン・チタン合金
優れた金属「チタン」軽量・比強度・生態的合成・非磁性といった優れた特性と、 環境に優しいリサイクル指数の高さが魅力の金属です。 当社ではチタン・チタン合金・形状記憶合金(Ni-Ti)を扱っております。
【特徴・用途】
特徴 | 用途 |
---|---|
軽量・高強度・高耐食 | 【航空・宇宙】 機体構造材、エンジン部品 他 【自動車】 バルブ、スプリング、コンロッド 他 【船舶・海洋関連】 各種部品 他 【化学・石油化学】 NaOH電解用電極、各種製造装置 他 【火力・原子力関連】 熱交換器、再処理装置 他 |
ファッション性 | 【スポーツ】ゴルフ、テニスラケット、自転車 他 【装飾】 メガネ、アクセサリー、時計 他 |
無毒性・生体適合性 | 【医療】 医療機器、人工骨、歯根、心臓弁 他 【食品】 整水器用電極 他 |
形状記憶合金・超弾性 | 【自動車】 燃料噴射弁用センサー 他 【装飾】 ブラジャー 他 |
【機械的性質】
鋼種 | 引張り強さ N/㎟ | 伸び % | 熱処理条件 |
---|---|---|---|
Ti 1種 | 270~410 | ≧27 | Annealing |
Ti 2種 | 340~510 | ≧23 | Annealing |
Ti 3Ai2.5V | ≧620 | ≧15 | Annealing |
Ti 6Ai4V | ≧860 | ≧10 | Annealing |
β15.3.3.3 | 700~820 | ≧26 | Annealing |
製品仕様
ワイヤー(チタン・チタン合金)
サイズ | 引張り強さ | 直径公差 | 真円度 | 表面状態 |
---|---|---|---|---|
φ6.0~1.0 | 機械的性質内調整可 | .0.02以内 | 3μm以下 | 酸化膜あり・酸洗・研磨・陽極酸化 |
φ0.9~0.1 | 機械的性質内調整可 | .0.01以内 | 3μm以下 | 酸化膜あり・酸洗・研磨・陽極酸化 |
φ0.09~0.05 | 機械的性質内調整可/td> | .0.005以内 | 3μm以下 | 酸化膜あり |
バー(チタン・チタン合金)
サイズ | 引張り強さ | 直径公差 | 真円度 | 表面状態 |
---|---|---|---|---|
φ6.0~4.0 | 機械的性質内調整可 | .0.02以下 | 3μm以下 | 伸線後直線カット |
2μm以下 | センタレス研磨 | |||
φ3.9~0.7 | 機械的性質内調整可 | .0.02以下 | 3μm以下 | 伸線後直線カット |
.0.01以下 | 2μm以下 | センタレス研磨 | ||
φ0.6~0.3 | 機械的性質内調整可 | .0.005以内 | 2μm以下 | 伸線後直線カット |
※長さ φ6.0~2.0 3000mm以下 φ1.5~1.3 1500mm以下 φ1.2以下 1000mm以下
当社製品特性および精度の他社との違い
【1】特性について
引っ張り強さとは破断限界を見るためのパラメーターで降伏点と合わせて使うことで、材料の持つ「強度」を見る為の指数です。
チタン・チタン合金、その他の金属材料には各々上記表に示されているように基準値があります。
通常の製品は、なまし材、硬材の2種類の仕様になりますが、弊社においては基準値内での引っ張り強さを伸線加工における加工硬化及び熱処理の条件等にて、お客様のご希望にあう条件で製造いたします。
【2】精度について
ワイヤー・バー材についての精度は、直径に対しての公差・真円度を求められます。
・直径公差とは、製品完成時の直径寸法の許容範囲を示します。
例)φ3.0mm±0.2 → 実測値 φ2.980~φ3.000以下
公差が狭くなるほど加工の難易度は高くなります。
・真円度は、断面の真円の値となります。
例)真円度 φ3.0に対し 10μm(楕円) → 5μm → 0μm(真円)
・直径公差・真円度は、ワイヤー製造における、伸線加工工程で確定します。
●金属素材のワイヤー製造の方法は、大きく分けて二通りあります。
【①ローラーダイスによる圧延方式の伸線方法】断面に対し2方向あるいは3方向のローラーによりワイヤーを細く引き伸ばしていきます。
<メリット> ・チタン等の伸線加工が素材のまま加工ができ、仕上がり品の表面は酸化物等が無いため表面処理が安価で行えます。
<デメリット>・コスト的に、後に説明する穴ダイスと比較すると1サイズのローラーが高価になります。
・ローラーの構造上、合成が弱いため硬鋼材の加工には不向きです。
・寸法精度は、JIS規格の範囲が限界となります。
・ローラーダイスの製造限界の為、ワイヤー最小線径もφ0.5mmとなります。
【②穴ダイスによる冷間伸線方法】ステンレス系、鉄系、銅系等のあらゆる金属のワーヤー製造に用いられています。
<メリット> 穴ダイスは材質として超鋼・ダイヤモンドの2種類がありますが、ローラーダイスと比較し、加工率が1枚で15%取れるのに対しローラーダイスは3%程度の為、ダイス費用がかなり安価となります。
例)φ3mm代の加工率15%であれば、ダイヤモンド穴ダイスとローラーダイスを比較すると50分の1となります。
ダイスメーカーの技術の進歩に伴い、線径精度・真円度精度も向上し、ステンレス系等は現在直径φ15μm前後の製品化が実現されています。
<デメリット> チタン・チタン合金・その他レアメタルの金属親和性の高い材料は、被膜を付けないと伸線できないことから、伸線用表面被膜加工技術のあるメーカーに限られています。
当社における製品製造
【1】ワイヤー製造について(チタン・チタン合金)
●伸線方法は冷間穴ダイス伸線を用いて加工を行っています。
仕上がりサイズ:φ0.05~φ6.5も範囲以内であれば0.01mm刻みで製造可能
例)φ1.15 φ2.74 φ0.55(公差の確認は必要)
1)加工素材入手後受入検査
→ 疵が発見された場合(メーカーと協議の上)内製でのピーリング加工(逆さダイス)にて除去
2)独自の表面処理加工
3)仕上げ線径に対し穴ダイス(超鋼・ダイヤモンド)にて適性な加工率のもと加工
仕上げ線径については、JIS規格サイズはもとより、受注先様独自のサイズ加工も行っています。
4)製品特性
→ 一般的な特性はもとより、材質の持つ特性範囲以内であれば加工硬化と熱処理の条件に基づきお客様の希望に対応しています。
5)表面処理
→ 一般的には、「酸化膜あり(黒皮品)」「酸洗いによる被膜なし(白肌品)」「ロール圧延上品」の3種類ですが、
|当社においては…
①伸線上がり
→ 伸線後伸線時の被膜材を除去し、熱処理加工仕上がり寸法精度重視線径に対し、5μm以内の精度を可能。
・可能な製造サイズ:φ0.05~φ6.5
②酸洗仕上がり
→ ①の製品を酸洗処理にて酸化膜を除去した製品。寸法精度ワイヤー内で3から5μmのばらつきとなりますが、線径に対しては10μm以内可能。
・可能な製造サイズ:φ0.1~φ6.5
③陽極酸化被膜
→ ②の加工後電解処理を行い、意図的に酸化被膜を付けます。精度は②同等で、大気中の酸化膜とは異なり、外しやすく次加工の圧延加工、プレス加工の焼き付き防止・金型の保護のために用いたり使用されています。陽極酸化は7色の発色ができ、装飾品等のニーズがあります。
・可能な製造サイズ:φ0.1~φ6.5
④研磨仕上げ
→ 独自の研磨方法により、Coil To Coil の研磨加工を行います。研磨取り代をを想定し、伸線後研磨に酸化膜を除去し、表面は金属光沢ある表面に仕上げま す。寸法精度重視線径に対し、5μm以内の精度を可能。
・可能な製造サイズ:φ0.1~φ6.5
【2】バー材製造について
●上記伸線方法において、ワイヤー製造後、一般的な機械的直線カットや材質の特性を生かしたテンションアニールによる直線材(直棒)を製造し、表面を処理します。
①伸線上がり
→ 伸線後、伸線時の被膜材を除去し、熱処理加工仕上がりを受注長さにカット。
・伸線ワイヤーのサイズのまま
②酸洗仕上がり
→ ①の製品を酸洗処理にて酸化膜を除去したワイヤーを受注長さにカット。ばらつきとなりますが、線径に対しては10μm以内可能 。
・酸洗サイズのまま
③陽極酸化被膜
→ ②の加工後電解処理を行い、意図的に酸化被膜を付けます。受注長さにカット。ばらつきとなりますが線径に対しては10μm以内可能。
・酸洗サイズのまま
④センタレス研磨
→ 仕上がりサイズより+0.06~0.15mm研磨取り代を足したワイヤーを製造し、直線カット後センタレス研磨加工を行います。
- 穴ダイス伸線によりワイヤー精度が高いため研磨取り代を低く抑えられます。
- これにより、加工回数の削減及び歩留まりを高められます。
- ローラーダイスによるワイヤーは、+0.2~0.3の研磨取り代を必要とします。(精度が悪いため)
例)・穴ダイス: φ4.1X2000L 50Kg→CG加工仕上 φ4.0X2000L(47.5Kg)
・ローラーダイス:φ4.2X2000L 50Kg→CG加工仕上 φ4.0X2000L(45.3Kg)
・仕上げサイズは同じでも、仕上がり重量は2Kg以上の差が発生します。
製品サイズ
直線カット加工 | |
弊社材料込み | |
サイズ | φ0.5~φ1.0 X 1000mmL |
サイズ | φ1.1~φ1.5 X 1500mmL |
サイズ | φ1.6~φ1.8 X 2000mmL |
サイズ | φ1.9~φ6.7 X 3000mmL |
※長さは一般的な最長サイズで材質により異なります。支給材においてはφ12mm以下可能。
センタレス研磨加工 | |
弊社材料込み | |
サイズ | φ0.7~φ6.5 X1000~3000mmL |
※仕上がり公差はJIS規格 h6以上はもとよりお客様のご希望に対し、5μm以内の公差対応可。支給材においては、直径φ30mm以下。長さ4000mm以下加工可能。